Solar energy is obviously one of the key renewable energy resources available to us. At the same time researchers are hitting against a glass ceiling. A famous 1961 paper by William Shockley (who co-invented the transistor) and Hans Queisser comes to the conclusion that for a semiconductor such as silicon the maximum conversion efficiency of solar energy into electricity will never be more than about 30%.
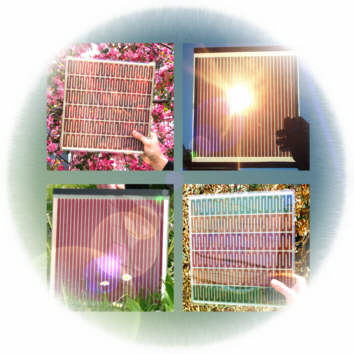
Dye-sensitized solar cells. A design similar to these solar cells is now used to demonstrate the creation and extraction of multiple charge carriers per photons.
One reason for this limit is that each light particle only excites one electron. Even if the electron has enough energy to excite two electrons, all this energy is lost and only one electron is excited. And this is the case for pretty much all present commercial solar cell technology. Fortunately, however, there are possible exceptions. Bruce Parkinson and colleagues from the University of Wyoming in the USA have now built a photovoltaic cell that at certain wavelengths of light can generate more than one electron per photon of light. Their approach promises to beat the Shockley-Queisser limit and could lead to solar cells with considerably enhanced efficiency.
In silicon and other semiconductors, if a photon excites an electron all excess energy is predominantly lost as heat. Of course, there are attempts to harvest the heat generated in solar cells, and such approaches could beat the Shockley-Queisser limit. And so could nanostructured materials that use for example plasmonic effects. But a more direct solution would be if the excess energy could be used to excite more than one electron in the first place.
October 4, 2010
5 Comments